Column Traditional Japanese woodwork techniques
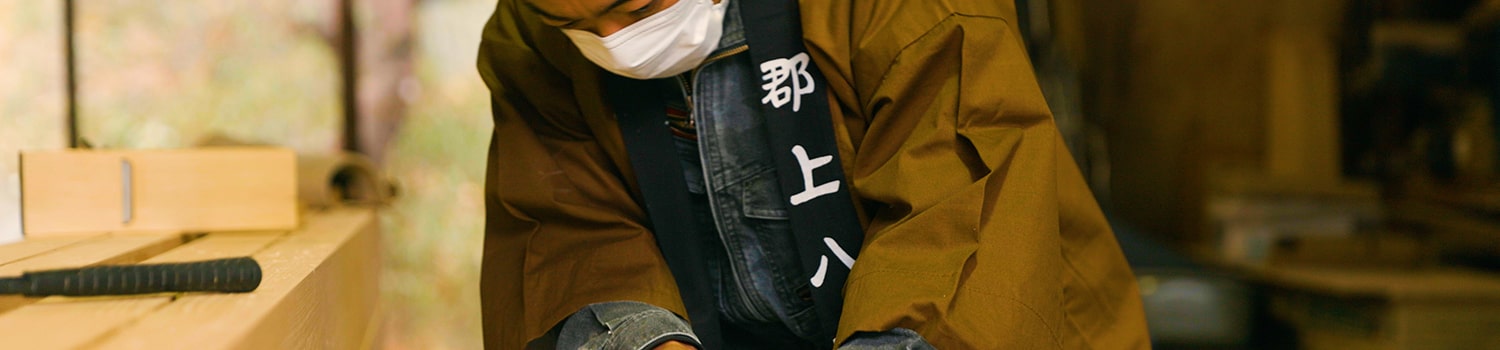
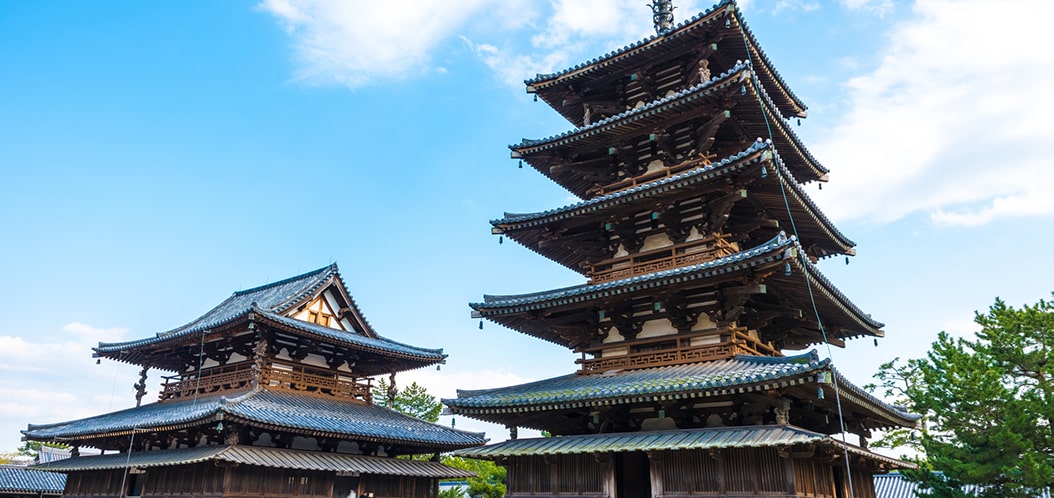
Traditional Japanese woodwork techniques
The world’s oldest wooden structure, Horyu-ji Temple, exists in Japan and is designated as a World (Cultural) Heritage site. It is said to have been built in 607 A.D., making it the oldest existing wooden structure in the world, dating back more than 1,400 years.
Horyu-ji Temple is a Buddhist temple. It is said that Buddhism, which originated in India, was introduced to China and then to Japan via the Korean Peninsula around A.D. 538 or A.D. 552. At that time, Buddhist monks and temple builders crossed over to Japan from the Korean Peninsula along with Buddhist teachings. They understood the characteristics of Japanese wood and considered Japan’s climate and earthquake-prone environment in building temples and shrines.
In A.D. 578, predating Horyu-ji Temple, three carpenters who came from the Korean peninsula built a temple called Shitenno-ji. Organized by one of the three, Shigemitsu Kongo, the carpenters not only built Shitenno-ji Temple but also participated in the repairs and construction of other temples and shrines.
Their activities have continued through the ages as a construction company in the modern era, and they are still in existence as the oldest company in the world: Kongo-Gumi Co., Ltd.
The Miyadaiku and their techniques
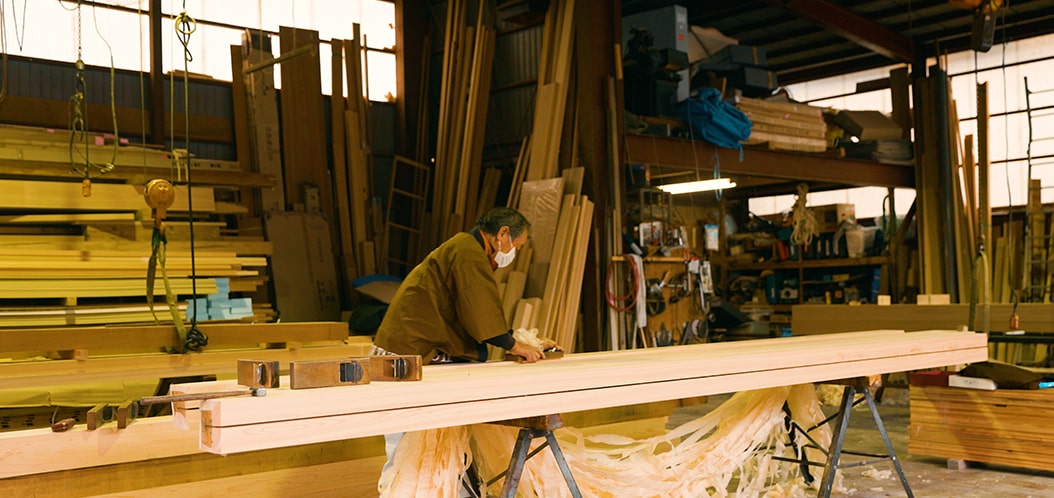
Carpenters like Kongo-Gumi, who build and repair temples and shrines, are called “Miyadaiku (a specialist in building religious structures)” in Japan. Since Miyadaiku are involved in constructing and repairing culturally valuable buildings such as World Heritage sites, national treasures, and buildings designated as cultural properties, they are required to have a wide range of knowledge and advanced skills, including architectural, religious and historical knowledge.
In particular, these carpenters must spend more than 10 years to master the “Kigumi Koho (wood joinery method),” a technique of constructing a building framework by cutting into the wood and fitting it together firmly, using almost no nails or metal fixtures. The method is necessary because wood is more resistant to earthquakes when assembled with other wood than when assembled with nails.
Japan is known worldwide for its frequent earthquakes. Wood has a certain degree of durability even when subjected to the bending force of an earthquake tremor. Furthermore, it can deform to some extent and release force when subjected to extensive vibrations from earthquakes because of its ability to restore itself to its original state.
When building large, tall temples and shrines, it is better to use the elasticity and resilience of wood to absorb the force than to use nails or other means to secure the wood to one another and make the structure as resistant to quakes as possible.
In addition, a stone called “Soseki (foundation stone)” is used as the foundation of the building, and the pillars are erected on top of it. Hence, when the building is shaken by an earthquake, as the soseki and the pillars are not fixed to each other, they disperse the force of the shaking by shifting against one another. Soseki also prevents moisture from being absorbed into the wood from the ground, making the wood less susceptible to rotting.
The techniques of the Miyadaiku were the starting point for Japan’s earthquake resistance, vibration isolation, and vibration control technologies, which have been passed down to the present day.
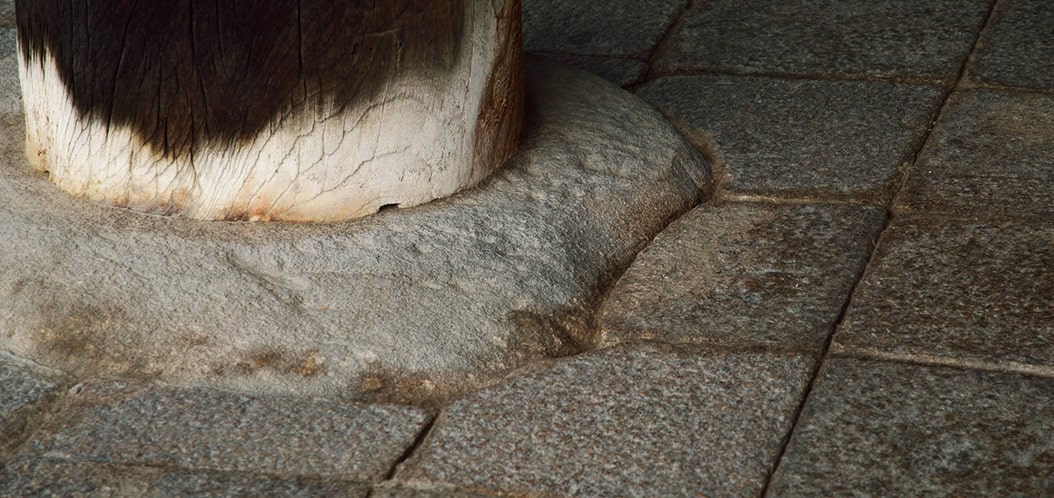
The lumber used for “Kigumi (wood joinery)” is not pre-manufactured in a factory, but rather is cut by hand on-site. In doing so, the carpenters read the growth conditions of the trees and the features of each piece of lumber to determine what kind of use the lumber is suited for. Then, using techniques known as “Tsugite (splicing joints)” and “Shikuchi (connecting joints),” the lumber is solidly connected to its counter piece.
Tsugite (splicing joints) is a technique used to join two or more pieces of wood together when they are not long enough to be used as is. There are around 70 types of tsugite, including “Koshikake-kamatsugi,” “Daimochi-tsugi,” and “Okkake-daisen-tsugi.”
These techniques require complex knowledge, like putting together a puzzle, as well as the skill to cut the wood to precise measurements. Once the pieces of lumber are inserted into one another, the result is so elaborate that the intricate joints are almost imperceptible from the surface.
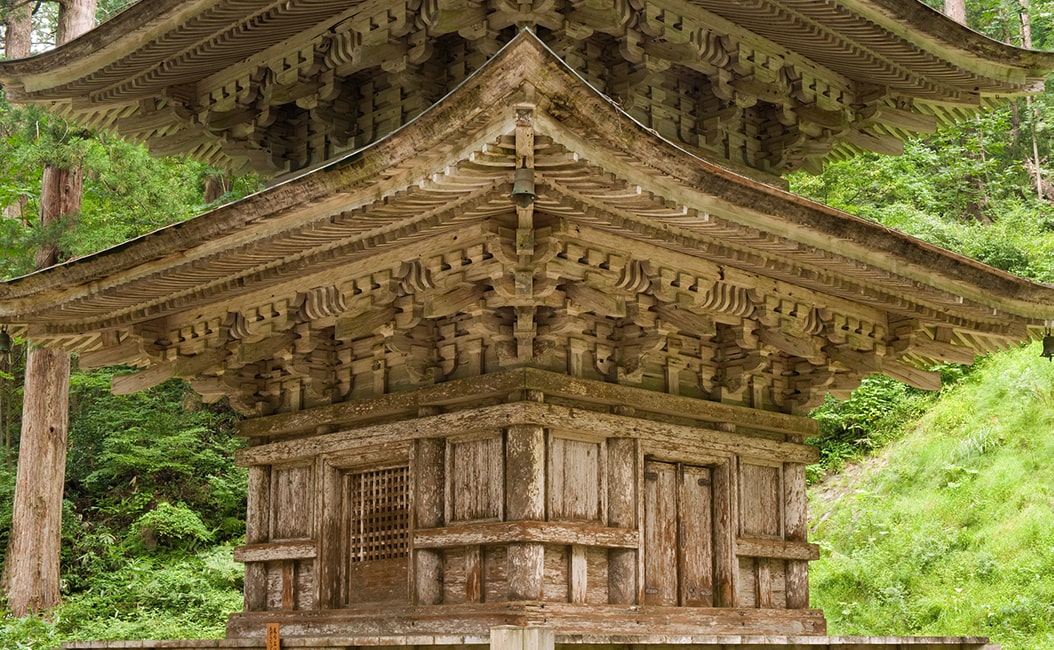
Shikuchi (connecting joints) is a technique for joining two or more pieces of lumber at a certain angle, for instance, at the joint between the post and the “hari (beam).” These are also those referred to as “Kabutoari-kake,” “Oireari-kake,” and so on. There is also a technique referred to as “Kiku-jutsu,” which involves using various rulers to precisely lay the lumber at various angles. It is said that it takes more than 10 years to master these techniques.
Japanese woodworking tools
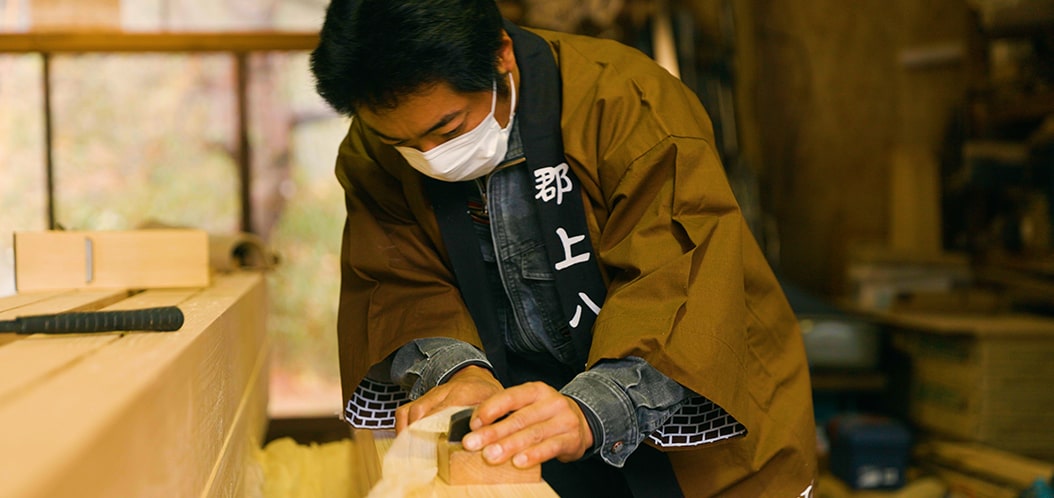
Japanese woodworkers use various tools, including axes, machete, planes, saws, chisels, and rasp files. Among these, the plane plays a very significant role.
Planes are used to plane the surface of the wood. Planes can be found worldwide, and while most planes in other countries are used by pushing against the wood, Japanese planes are used by pulling against the wood. Nowadays, electric planes are also available, and they have become an indispensable tool for woodworking all over the world.
Nevertheless, in Japan, planing has another vital purpose besides flattening the surface of lumber. It is used to very thinly plane the surface of the wood, giving the lumber a distinctive luster and shine.
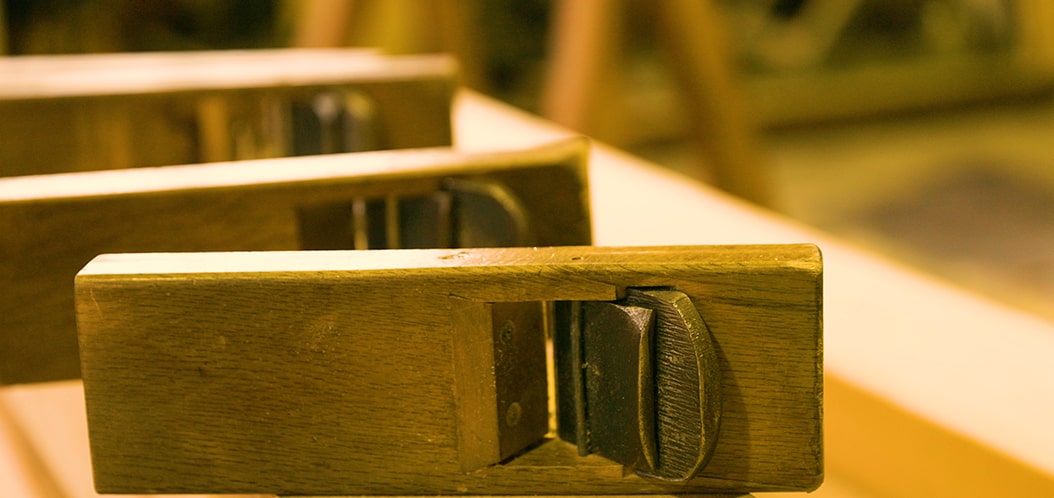
Hinoki, often used as a building material for shrines and temples, is a homogeneous, dense white wood with no visible annual rings, so planing gives it a silky white shine. The planed Hinoki has a gorgeous natural beauty even in its natural state, even in the absence of painting or other processing.
In contrast, Sugi and other woods also become very exquisite building materials when planed, as the grain of the wood becomes more pronounced and shiny. This is evidence that the Japanese have long inherited and utilized techniques that maximize the essential beauty of wood, based on a thorough understanding of their features.
Column
-
Introduction: Japan’s land and its wood culture
-
Traditional Japanese wooden homes that can withstand severe climates and earthquakes
-
Features of Japanese trees and timber
-
Features of Japanese homes and wooden furniture
-
Durability, fire resistance, seismic resistance, and termite-repellent features of Japanese lumber
-
Traditional Japanese woodworking techniques
-
Modern Japanese woodworking techniques