Column Modern Japanese woodworking techniques
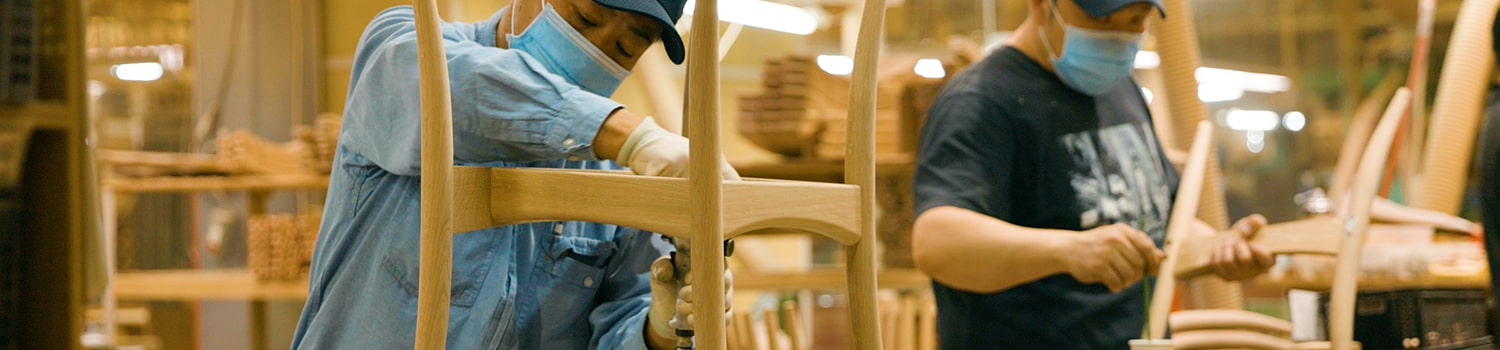
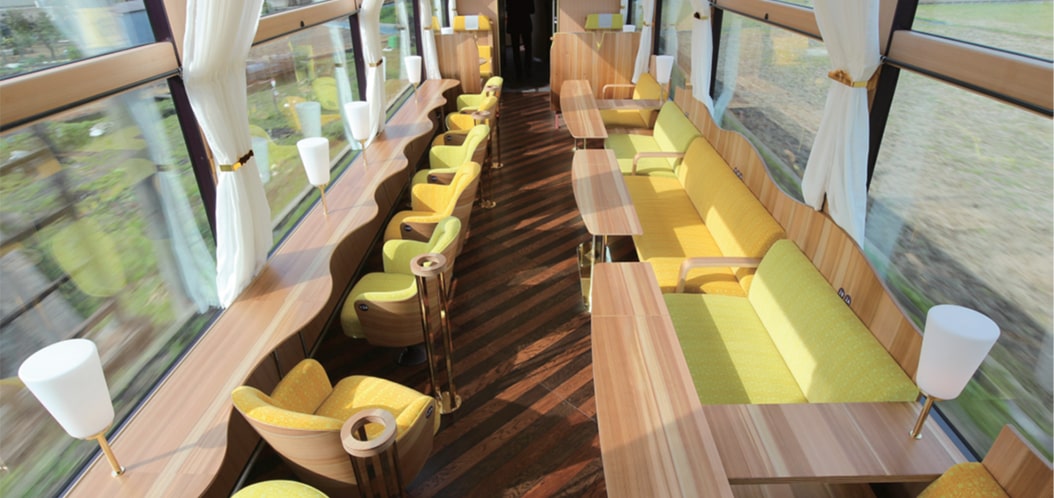
Modern Japanese woodworking techniques
For around 215 years, from 1639 to 1854, Japan severely restricted trading and exchange with foreign countries. During this period, Japan’s woodworking technology, which had been passed down from generations, was further developed, and a wide variety of woodworking products, from tableware, cooking utensils, furniture, and other daily utensils to artistic and cultural items, were created using local wood throughout the country.
Even today, there are many woodworking regions throughout Japan, and it is said that there are more than 80 traditional crafts using wood alone.
Typical woodworking techniques include “sashimono,” “choukoku (carving/engraving),” “kurimono,” “hikimono,” “magemono” and “tagamono (cooperage),” all of which are still practiced today.
Sashimono
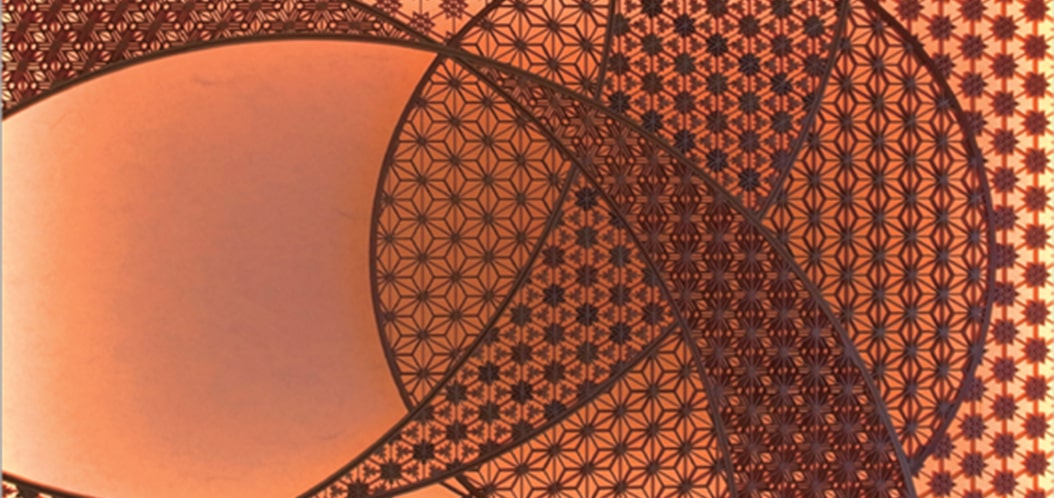
Sashimono is a technique for making chests, shelves, and boxes using only wood alone and without any joining tools such as nails. Mortises or grooves were carved into the wood to join two boards to make chests, shelves, and boxes. It is said that there are more than 1,000 types of “Kumite,” a method of assembling wooden boards.
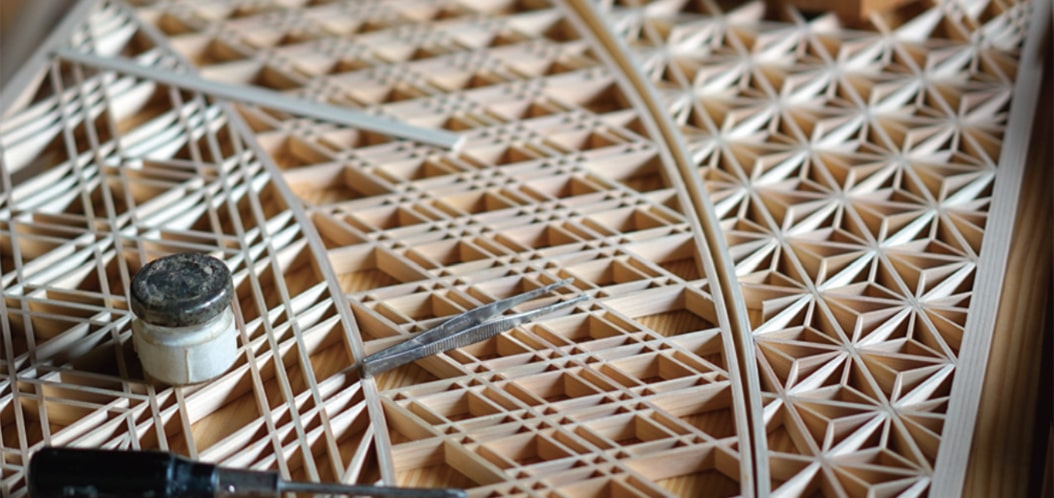
Chokoku (Carving/engraving)

In Japan, there is a type of interior decoration called “Ranma (transom)” in which carved wooden open structure panels for the purpose of lighting, ventilation, and decoration, are inserted above “shoji (sliding outer partition)” and “fusuma (sliding door),” which serve as partitions between rooms or between rooms and corridors.
Chokoku (carving/engraving) is also often used for signboards, furniture decoration, Buddhist statues, and Buddhist ritual implements, and techniques include “Maru-bori (round carving),” “Uki-bori (relief carving),” “Shizume-bori (sunken carving),” and “Sukashi-bori (openwork carving).”
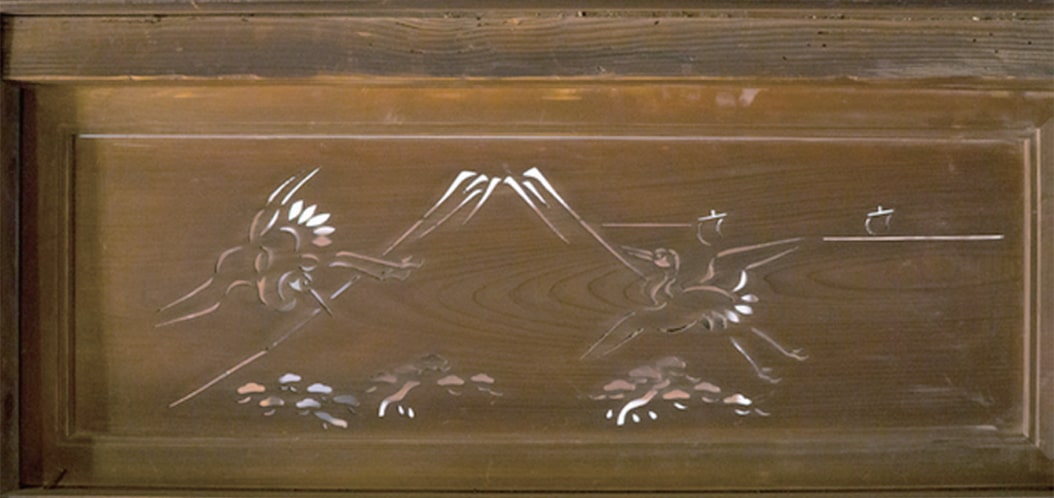
Kurimono
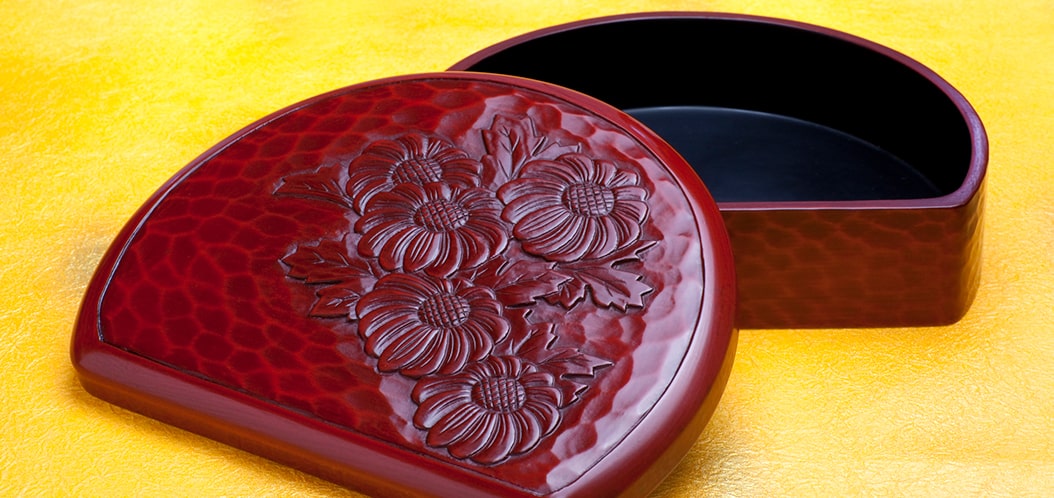
This is a technique of hollowing out a block of wood with a carving knife or chisel to create the intended shape. This technique can create complex curves and rounded shapes at will and is used for wood products that emphasize their curves, such as tableware and trays for carrying food.
Hikimono
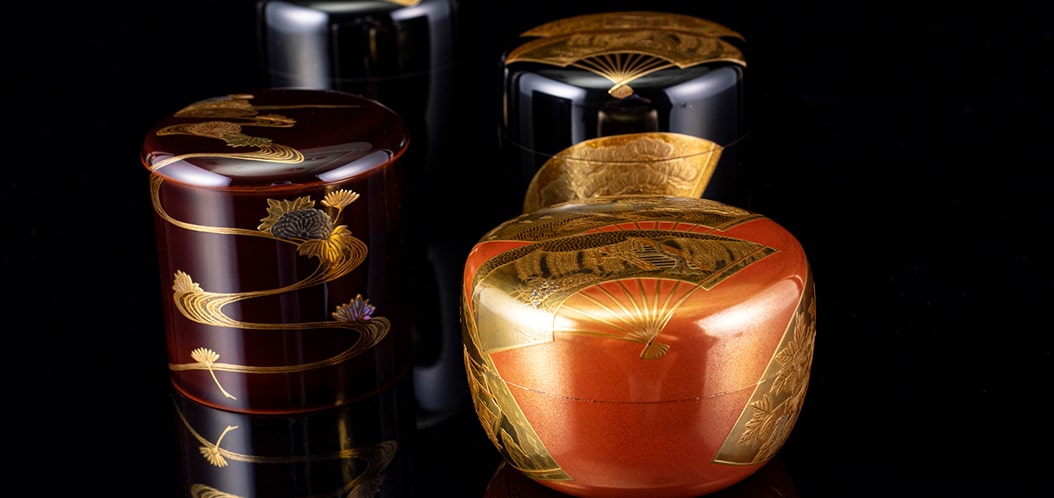
This technique is used to create a shape by applying a blade to wood turned on a potter’s wheel. This technique is suitable for making circular bowls, owan (bowls), and other items that can be formed into various shapes depending on the angle and the way the blade is applied.
In Japan, this technique is said to have been established roughly 2,000 years ago, and wooden cups and bowls made with the hikimono technique have been excavated from old ruins. Tableware made with the hikimono technique is often coated with “urushi (lacquer)” and used as lacquerware, often exported from Japan to the rest of the world.
Magemono
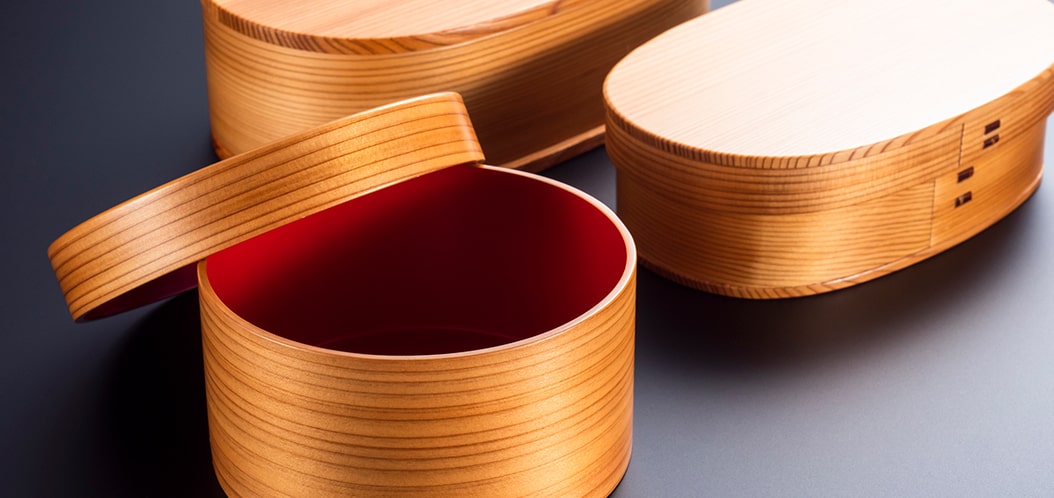
This technique is used to make containers and other objects by bending thinly sliced wood such as Hinoki and Sugi into circular shapes. There are several techniques for bending wood, such as “Kiri-mage (lancing),” which uses a small knife to bend the wood, “Hiki-mage,” sawing with a thin saw to bend wood, “Yu-mage,” soaking wood in hot water to bend it, and “Mushi-mage,” bending by steaming the wood.
In modern days the most common techniques used are yu-mage and mushi-mage. They are used to make various containers, such as barrels, pails, and lunch boxes.
Tagamono
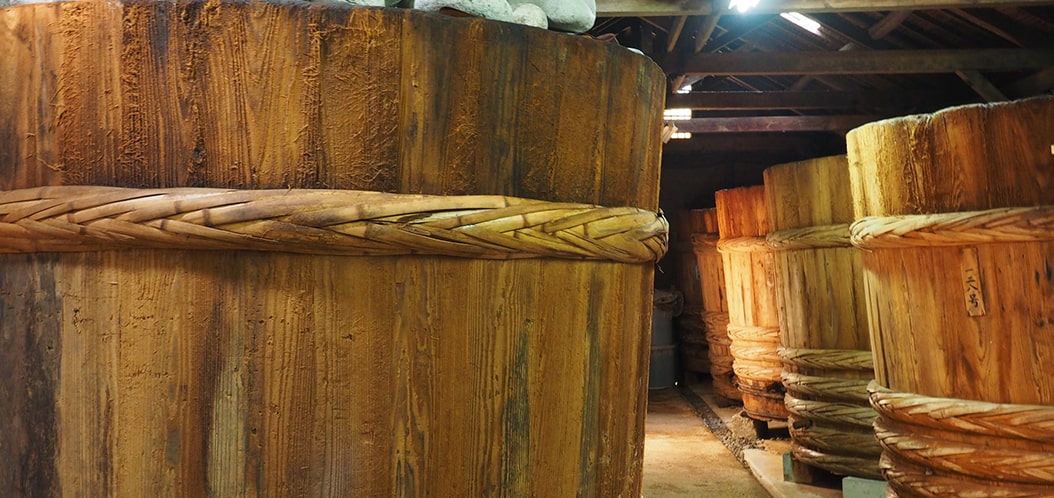
With this technique, boards are arranged in a circular pattern and tightened with a “taga,” a fastening device made of bamboo or metal, to form a container. Since, unlike magemono, thicker and stronger wood could be used, making barrels and pails with greater durability was possible.
This technique has led to a dramatic development in the production and distribution of sake, soy sauce, miso, and other fermented foods that Japan prides itself on, as they can be stored for long periods and transported as is.
Making of western furniture leading to the modern era
After 1854, Japan rapidly adopted and developed the cultures of Western countries such as the United States, Great Britain, France, and Germany. Western furniture, which had not been common in Japan until then, was incorporated into daily life.
The lifestyle of sitting on “tatami” and eating at a “zataku (low table)” was replaced with chairs and dining tables. Moreover, the lifestyle of sleeping on futons directly placed on tatami was replaced with beds. Sofas, cushions, and low tables were also placed in the living room. At first, these pieces of furniture were imported from overseas, but as their use gradually spread to ordinary households, they began to be made in Japan.
The people responsible for making Western furniture in Japan were the carpenters and traditional woodworkers who had inherited the Japanese wood culture. They evolved into unique Japanese furniture makers by successfully integrating Western tools and the latest technology with wood processing skills and decorative techniques such as “urushi-nuri (lacquering),” which they had cultivated over the years.
Magegi
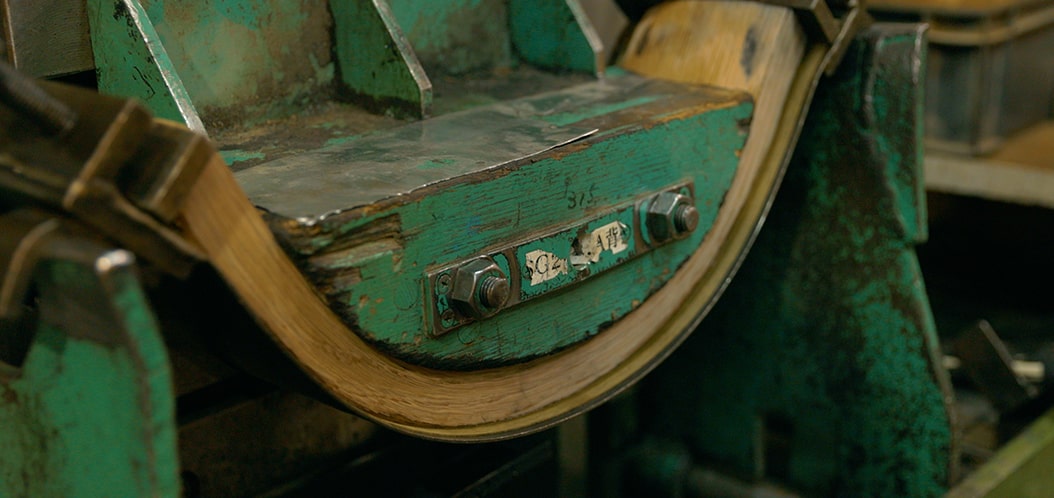
“Mageki-kagu (curved wood furniture)” was invented by German and Austrian furniture maker Michael Thonet around 180 years ago, using the method of steaming and bending wood. The technique involved soaking wood in water or exposing it to steam to moisten it, bending it with heat or pressure, fitting it into a mold to dry, hardening it, and shaping it into curved shapes and patterns.
Since a similar technique of magemono, a Japanese woodworking technique, such as yu-mage and mushi-mage, had been handed down for roughly 900 years, it is believed that these techniques were easily accepted by artisans who began making Western furniture in Japan. The Tohoku region of Japan and the Hida region of Gifu Prefecture, located near the center of Japan, are famous for producing mageki-kagu.
The human body has no straight parts and is rounded in all areas. Thus, the curved shape of the magegi has a gentle and fitting touch to the human body providing a comfortable feel.
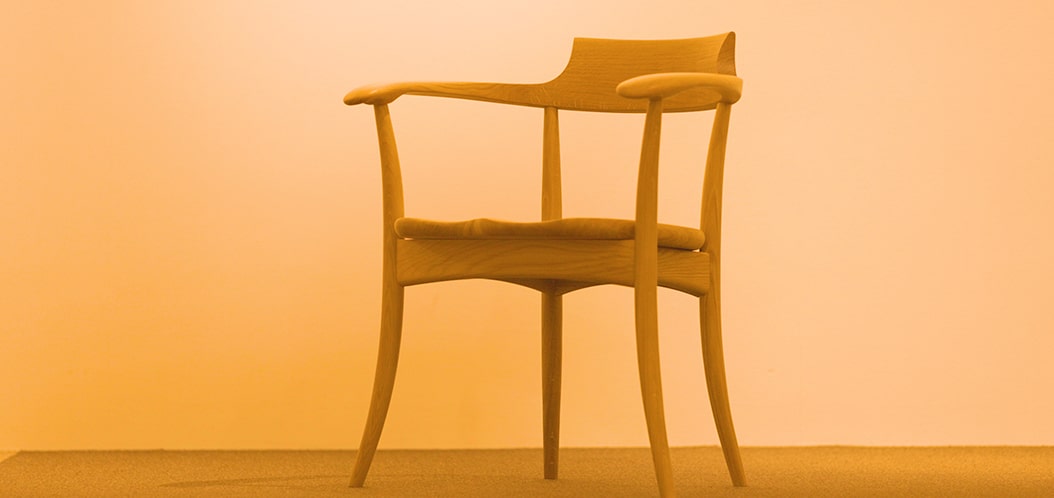
Seikei-gohan (Molded Plywood)
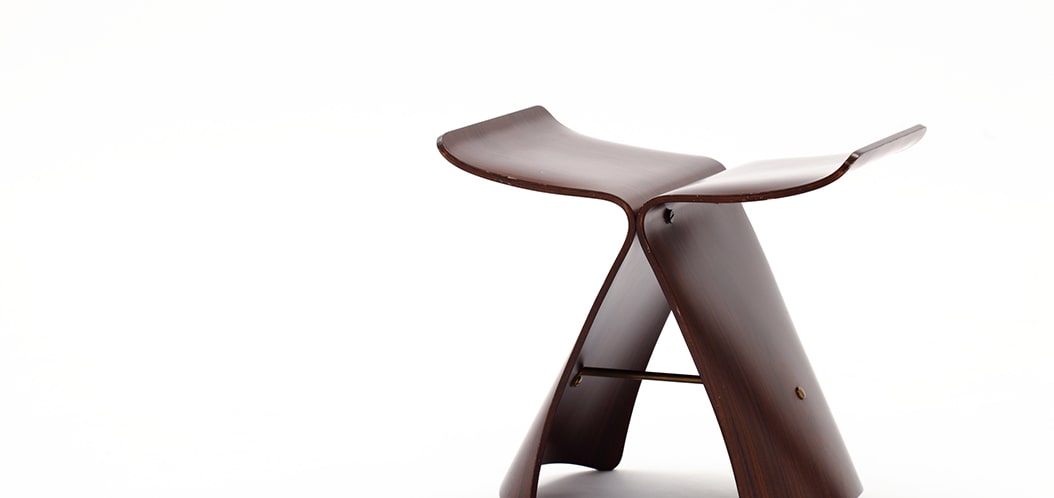
This is a woodwork technique in which thinly sliced pieces of wood are stacked one on top of the other, glued together, and then shaped into a curved surface through molding while applying heat. This technique is mainly used for chairs and is a manufacturing method that prevents distortion and curvature. The products are light and sturdy and can be formed into complex curves that would be difficult to achieve with solid wood.
Japan’s technology of seikei-gohan (molded plywood) is so advanced that designers worldwide have been able to realize and commercialize the intricate curved structures they envision.
In addition to its intricate curves, seikei-gohan is characterized by the beauty of its surface grain. The grain of the thinly sliced wood shows itself as it is, allowing the original beauty of the wood to be enjoyed. In recent years, seikei-gohan made from Sugi and Hinoki has also started to be produced and is expected to become more prevalent going forward.
This technique was introduced to Japan after World War II with the country’s economic development. Light, durable, and beautifully grained seikei-gohan furniture has become widely used not only in homes but also in music halls, schools, stadiums, and other public places throughout Japan.
It is believed that the fact that it is so widely used despite the availability of cheaper plastic materials as alternatives is due to the Japanese people’s attachment to wood and the permeation of wood culture.
Other latest woodwork techniques
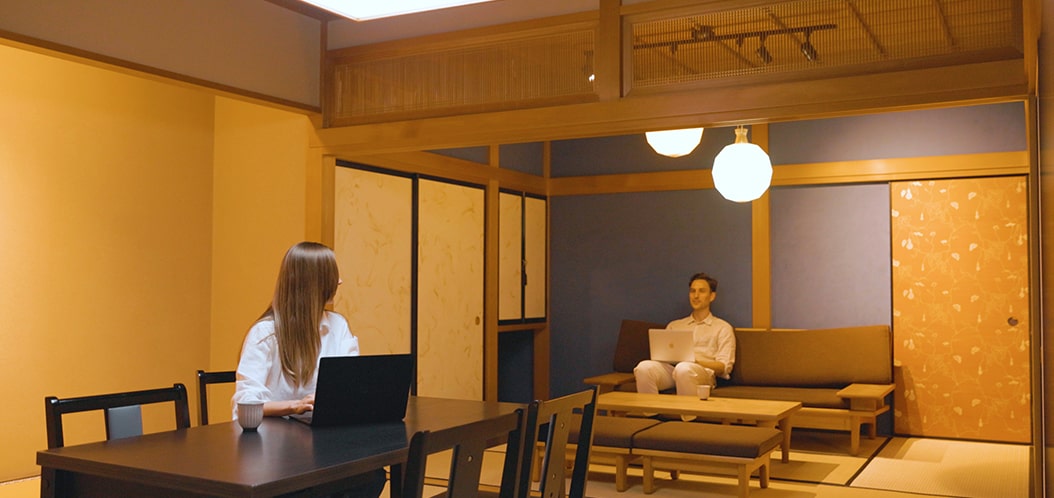
With the development of processing technology using the latest CNC cutting machines to cut solid wood into 3D shapes, it is now possible to mass-produce three-dimensional free-form curves from solid wood without using magegi or seikei-gohan.
Along with the use of such newly developed state-of-the-art technology, new Japanese furniture is being created by combining the advanced knowledge of Japanese craftspeople, who have long cultivated their skills in reading the growth conditions and properties of each type of wood, with sophisticated woodworking techniques.
It is said that Japanese furniture is characterized by simplicity of materials, an emphasis on spatial harmony, the use of natural materials, a clean look with few colors, and an overall low center of gravity. These features are said to have much in common with Scandinavian furniture.
Japan has approximately 25 million hectares of forests, with a forest ratio of roughly 66%, or two-thirds of the country’s total land. This is comparable to Finland and Sweden, known for having the highest forest ratios in the world.
Perhaps the similarities between Japan and these two countries can be attributed to their wood culture, in which trees have been used in daily life for many years, and history has been created together with the existence of trees.
Column
-
Introduction: Japan’s land and its wood culture
-
Traditional Japanese wooden homes that can withstand severe climates and earthquakes
-
Features of Japanese trees and timber
-
Features of Japanese homes and wooden furniture
-
Durability, fire resistance, seismic resistance, and termite-repellent features of Japanese lumber
-
Traditional Japanese woodworking techniques
-
Modern Japanese woodworking techniques